Actemium Powers TeCo CDC’s Packaging Transformation
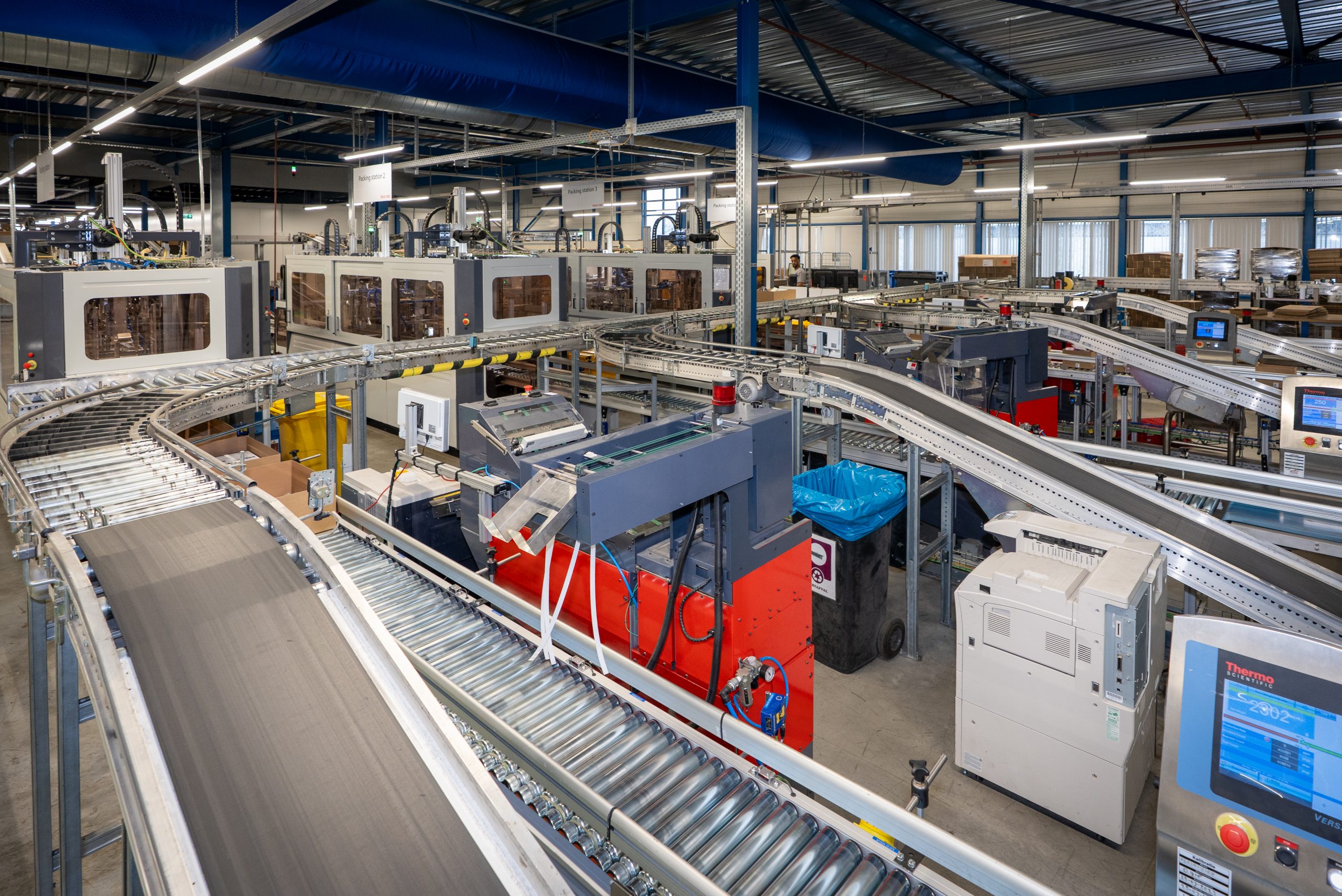
TeCo CDC, based in 's-Hertogenbosch in the Netherlands, is much more than a standard distribution center. It serves as the logistics hub for electronics companies Nedis and Distrelec, two major players in B2B and B2C electronic product distribution across Europe. Every day, over 12,000 customer orders are picked, packed, and shipped from its highly automated warehouse operation.
To maintain high throughput and prepare for future growth, TeCo CDC relies on three automated packaging lines. However, aging controls, data inconsistencies, and lack of system visibility led to a growing number of rejected boxes that had to be manually handled—more than 1,400 per day, or nearly 12% of total orders.
That’s when Actemium stepped in.
The Challenge: Too Many Manual Workarounds
TeCo CDC manages a massive inventory: over 177,000 SKUs, stored across 30,000 pallet locations and 160,000 red plastic bin locations. Customer orders are automatically packed into one of three box sizes, optimized to fit neatly into those bins.
But with corrupted data and system bugs causing a surge in rejected boxes, the team faced hours of daily manual work.
“We were spending up to 14 hours each day manually processing rejected packages,” recalls Martin Stienstra, Technical Project & Facility Manager at TeCo CDC. “And because the packaging machine controls lacked visibility, we had no way of diagnosing the issues ourselves.”
The Solution: Smart Retrofit with Siemens PLCs and WinCC
TeCo CDC turned to Actemium for help—not only because of our strong track record in industrial automation, but also through an existing relationship built on trust.
“They started with a pre-engineering phase to fully map our systems, needs, and interfaces,” explains Stienstra. “Then they presented a detailed action plan.”
The Actemium team replaced legacy controls with Siemens SIMATIC S7 PLCs, significantly improving system reliability and diagnostics. A middleware layer built on Simatic WinCC was added for seamless communication with TeCo’s WCS (Warehouse Control System), particularly enhancing the control of label printers—a key element of packaging precision.
Fast Execution, Timely Results
Timing was tight: the retrofit took place between September and November, a high-pressure period in the logistics industry due to peak holiday demand.
“Thanks to the close collaboration and trust between Actemium engineers and our in-house technical team, we completed the retrofit faster than expected.” says Stienstra
To support the upgrade, TeCo CDC even made in-house modifications to several conveyors, adapting them to the improved packaging flow.
“This retrofit wasn’t just a fix—it was a strategic upgrade,” concludes Stienstra.
It’s already delivering major cost savings, improving reliability, and preparing us for future growth in order volume. For us—and for our partners at Nedis and Distrelec—this has been a game changer.
- Rejects reduced from 1,400+ to just a few dozen per day
- Packaging process now fully transparent and traceable
- +20% increase in system performance and throughput
Looking Ahead
With smoother automation, greater insight into operations, and room to scale, TeCo CDC is now well-equipped to meet the evolving demands of fast-paced, high-volume logistics—proof that the right automation partner can truly transform your operational backbone.
Want to learn more?
Get in touch with our teams in the Netherlands!