We are helping you find answers to the new questions of Industry 5.0 around beer mix and the impact of ‘smart’ technologies on production and maintenance, as well as energy management.
Actemium’s insights and expertise can help you navigate your brewery’s or plant’s transformation into the future, bringing the right tools to address digitalisation.
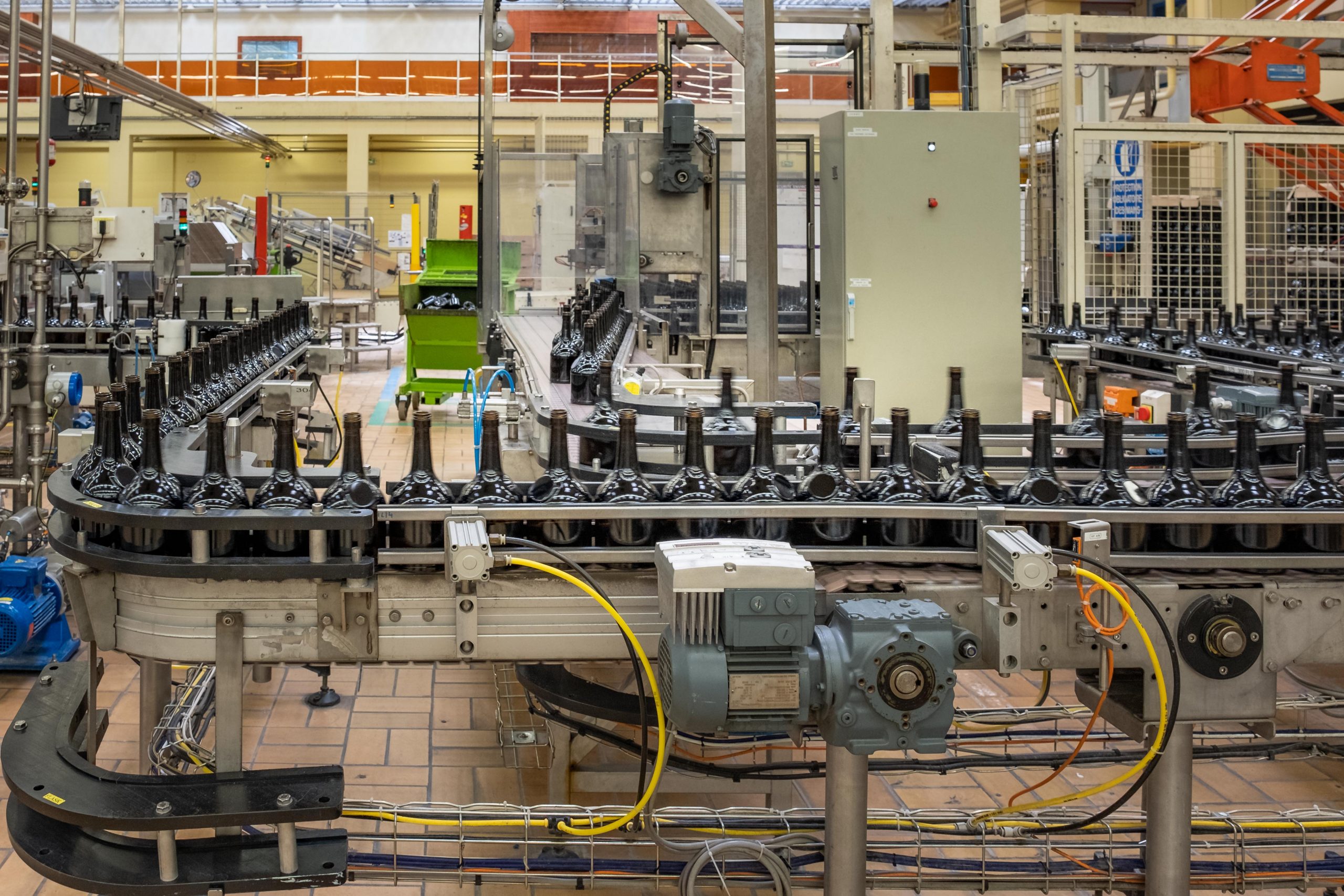
Smart Solutions for today’s and tomorrow’s industry
Actemium, a key player in the transformation towards the Sustainable Factory of the Future
Building on our agile network of experts, we innovate in order to support the longterm development of industrial customers, in a sustainable way. As a strategic partner, Actemium connects the dots within the value chain, on electrical, mechanical, automation and digitalisation levels, in order to accelerate the energy transition and digital transformation.
- Connectivity data
- Analytics & Intelligence
- Human machine interaction
- Digital – physical conversion
Besides in-house brewery solutions, Actemium also implements solutions as an integrator of process & MES technology platforms, combining segment knowledge with proven execution methodology in process control and MES.
Connect with Actemium's Experts
If you have questions or want to acces to our service click here!